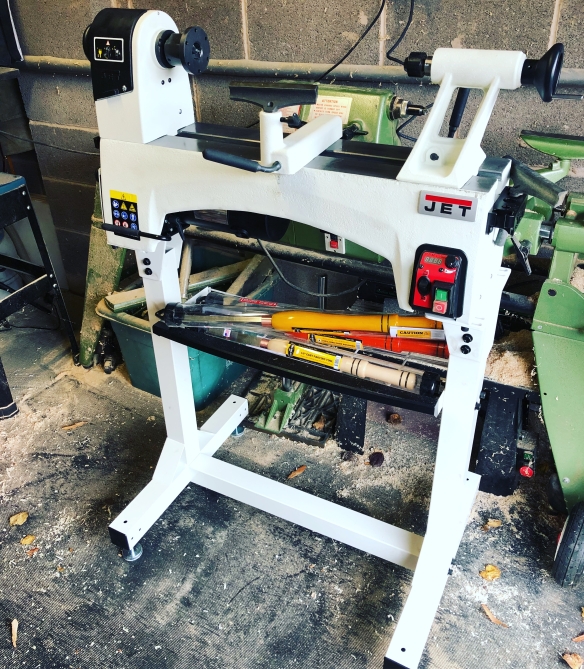
The lathe fits nicely on the Jet stand, but there’s no way to attach the stand extension if you hjave the extended lathe bed!
Last October I ordered a new Jet 1221vs lathe and bed extension. The Shopsmith had been a great first lathe, but I was after something more compact, and also at a much more comfortable height. After much indecision I decided to order the stand and stand extension Jet make specifically for the lathe – while it was extra financial outlay, I’m time pressured in the ‘shop at the moment, and building jigs or shop fixtures is something I generally don’t enjoy that much. So I decided to take the quick option and get a stand which I assumed would be good to go after following the assembly instructions.
That turned out to be a bigger assumption that I realised, because Jet have at somepoint in the past couple of years changed the design of their lathe stands, and neglected to inform Axminster (with whom I placed the order), or in fact any of their other UK stockists. After a frustrating evening of picking through the various parts, and reviewing conflicting sets of instructions, it turns out that Axminster stock the “new” style Jet stand, but the “old” design of the stand extension (and the stand extension is an essential purchase if you have the bed extenstion for the lathe). Rather unhelpfully, these two design iterations will not fit together without drilling and tapping new holes, which is not what I want after spending a decent amount of cash on a readymade solution. To be fair, Axminster were fantastic and kindly arranged for a courier to collect the stand and provided a full refund within days of my initial query. But that left me with a lathe and nowhere to put it. I called round every other UK Jet stockist, and they all reported the same stock issue, so this may be a consideration if you’re thinking of ordering a Jet lathe.
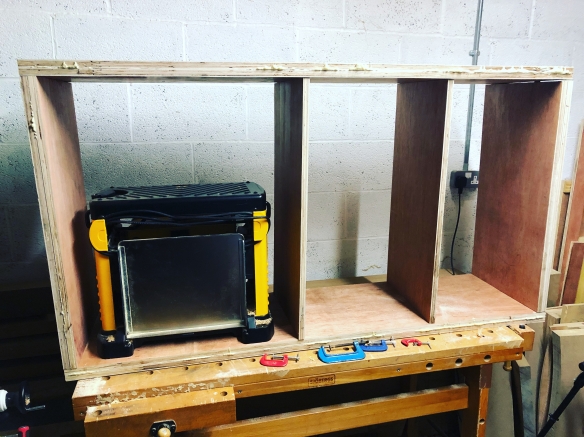
Dry fitting the internal dividers before assembling the stand
After several months of resting the lathe on my saw benches, I’ve got to the point where I need to reclaim some floor space for working on the larger elements of the Roubo bench. I played around with several ideas for suitable lathe stands, and while Rich was visiting for the Midlands Woodworking Show, we got talking about solutions. The key criteria for the lathe stand were that it had to offer mass and rigidity (no one wants a lathe dancing across the floor), to provide storage for my Dewalt thicknesser and other workshop kit (you can never have too much storage), and be quick to make.
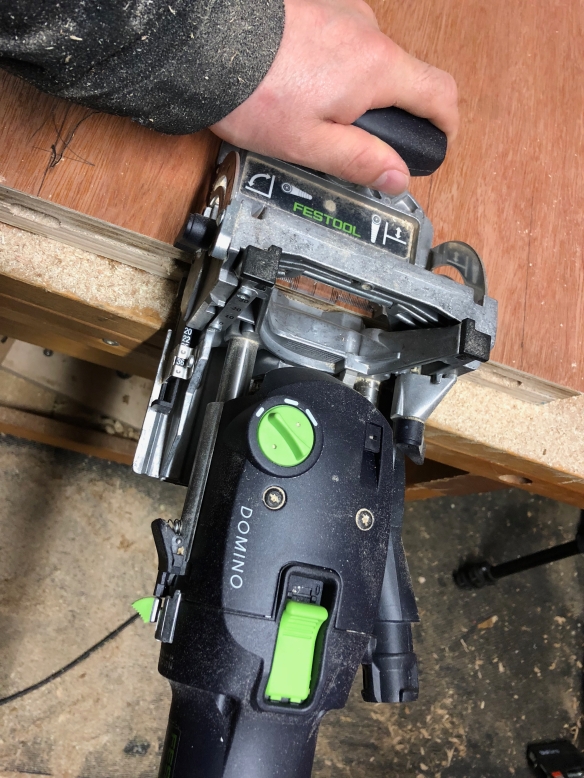
This build is held together with a bucketload of PU glue and 10mm dominos
We quickly came up with a 34″ high, 60″ long and15″ deep cabinet which could be made by laminating two layers of 3/4″ ply to achieve suitable rigidity, and the following weekend I found myself ordering more sheet material than I’ve ever bought in one sitting. There is nothing elegant about this build, but it has been a quick and effective way of solving an immediate storage problem. The ply was laminated using a bucketload of PU glue (horrible stuff, but perfect for this application), and the casework was then assembled using 10mm wide dominos. While I prefer handtools, the Festool Domino is a wonderful machine – intuitive to set up, dirt simple to use, and super effective.
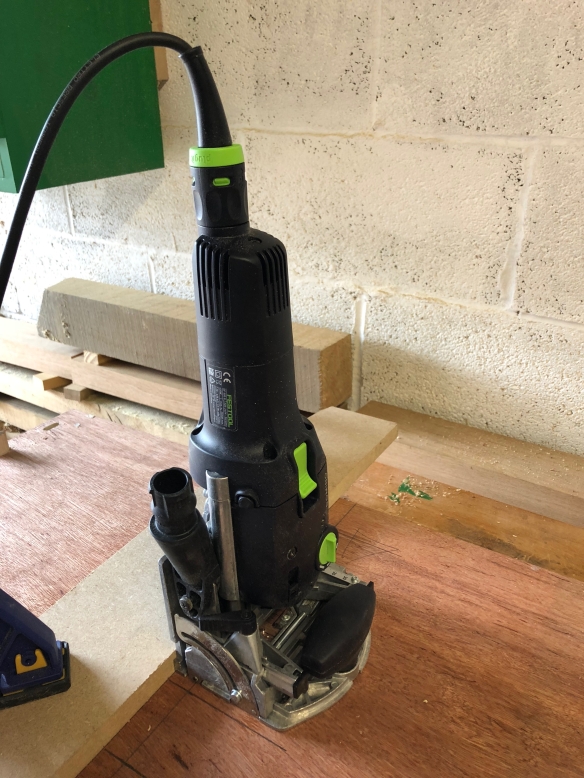
Cutting the domino slots for the dividers
To reinforce the casework and prevent the top sagging, I fixed horizontal backboards of 3/4″ ply to the rear edge of the top and bottom, again using dominos. A base of 1×2″ pine was rescued from my scrap pile, and fitted using more PU and a pneumatic nail gun (another great problem solver for workshop fixtures and DIY).
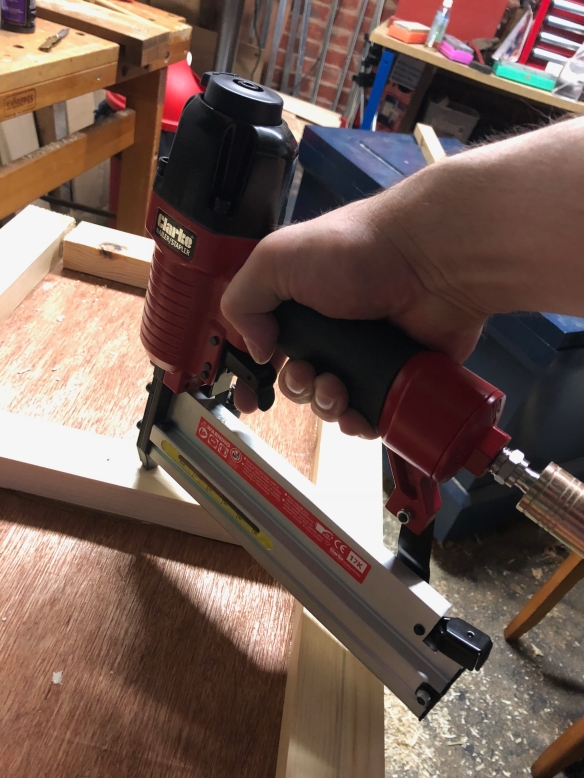
Fitting the base – more PU and a nail gun
The build only took a few evenings, and the most painful stage was actually decanting half of the workshop so that I could move the rubber flooring out of the way of the cabinet. The lathe fits comfortably on the stand, and so far there is no sign of any sag or movement under the weight of the machine. Storing the Dewalt in the cabinet adds further mass, and the two narrower compartments will be fitted with shelves and drawers on an as-needed basis. The only remaining work will be to clean up and paint the cabinet, and to drill mounting holes so that the lathe can be bolted to the top. I’ve not yet decided whether to fit a pine face frame – it would smarten the unit up plenty, but also add a reasonable further time investment to what is at the end of the day a workshop fixture. If you have strong opinions on face frames, then cast your votes in the comments!